With its low environmental impact, Murra Warra is the ideal location for a wind farm. Situated on 4,250 hectares of farmland used for sheep grazing and broadacre cropping, the footprint of the wind farm accounts for less than two per cent of the area. In addition to its minimal effects on agricultural productivity, Murra Warra was chosen for its consistently strong wind resources, close transport links, and an on-site connection to the grid network.
The Murra Warra wind farm is being developed in two stages at an estimated cost of $650 million and is expected to operate for 25 years. The construction of the $247 million stage one commenced in April 2018, and has been in operation since February 2020. Construction of stage two commenced in late 2020, and is expected to be fully commissioned and operational by mid-2022.
Featuring 38 General Electric (GE) Cypress 5.5-158 wind turbines, the Murra Warra II wind farm will generate enough renewable energy to power the equivalent of 150,000 homes in Victoria and offset around 500,000 tonnes of carbon emissions every year, playing a significant role in supporting the Victorian renewable energy target of 40 per cent by 2025. The power generated from stage two will be supplied to Australian electricity generation and retailing company Snowy Hydro under a power purchase agreement.
Murra Warra II will provide immense benefits for the regional economy, creating more than 400 full-time jobs during the two-year construction period and ongoing employment opportunities in operations, maintenance and project support services throughout its lifetime.
The completed wind farm will feature an operations and maintenance building, four permanent meteorological masts and car parking facilities.
The Turbines
Murra Warra II features 38 General Electric (GE) Cypress 5.5-158 wind turbines—one of the quietest systems in its class designed to operate at low to high wind speeds. The turbine blades are aerodynamically optimised and have serrations on the edges. Each blade is 70.5m long and weighs approximately 20 tonne. The weight of the nacelle is approximately 130 tonnes.
The turbines feature the next electrical system-(NES) gearbox-based concept, including an asynchronous generator and a fully rated converter, which permits stable grid feed-in. Each turbine has a large rotor with a 144m diameter, delivering a nominal output of 3.7MW. The hub height of each turbine is 139m and the total height to tip is 211m.
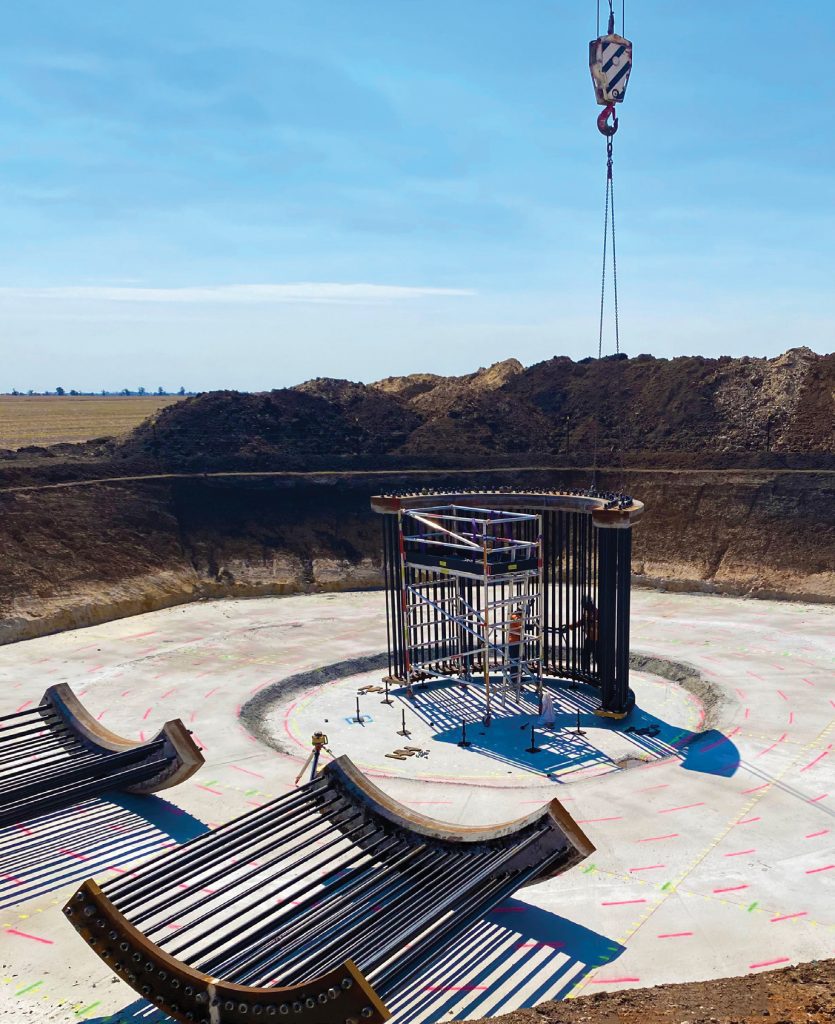
Robust Anchor Cage Solution
Given the size, scale and weight of the turbines, a robust anchor cage solution was required; the expertise of Allthread Industries was required.
Allthread Industries supplied the anchor cages, which included large plates and 176 M48 bolts, each of which was 3.8m long and weighed 50kg.
The principle contractor for the civil works was Australian-owned Zenviron in Newcastle. According to Simon Preston (Group General Manager, Allthread Industries and Precision Oxycut), Zenviron approached Allthread Industries to quote on the anchors, which were designed by icubed (a local engineering consulting firm).
“Nick Canto, the Principal Consultant from icubed designed gravity anchors for the project. So rather than being pierced onto any bedrock, the anchor is effectively an enormous mass of concrete and steel. The sheer weight of the anchor ensures that the tower remains stable, even under the force that the wind generates,” said Preston.
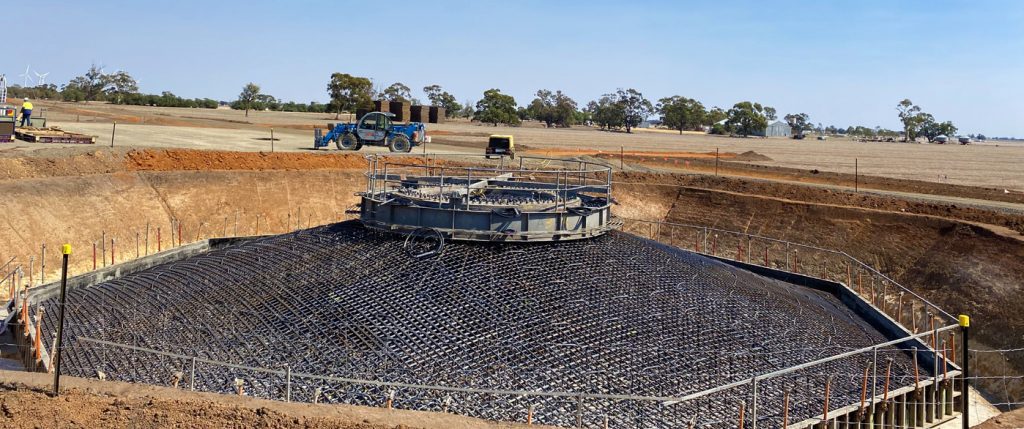
“To begin with, we were given a design to quote on, which featured an 80mm plate at the bottom. We knew our quote would be compared to overseas suppliers—that is quite common for us. While the client was keen to work with a local Australian manufacturer, we knew we’d have to sharpen our pencils.”
“On reviewing the scope, it became apparent that a key element was missing from the original tender request—the grout pocket forming ingots. These ingots form a trench that runs along the top of the foundation. When the tower is lowered into position, the trench is filled with grout so that the self-leveling material ensures that there is an even surface for a perfectly straight tower—it eradicates the danger of a Leaning Tower of Pisa,” explained Preston.
“Traditionally, the grout pocket trench is made using a set of rubberised foam ingots that is fitted around the bolts during assembly. They are quite significant in terms of size, very expensive and non-biodegradable. And they’re almost always made overseas. As the grout pocket forming ingots had been overlooked, the client asked Allthread Industries to supply these as part of the anchor cages,” said Preston.
Allthread Industries sourced prices for these rubberised foam ingots, and received quotes that were extremely expensive. In addition, Allthread Industries knew that the end result would be a significant volume of waste that simply could not be recycled and end up in land fill.
Instead, Allthread Industries investigated a more environmentally friendly alternative. This alternative called upon the expertise of their sister company, Precision Oxycut— the largest steel cutting and plate processing company in New South Wales.
“With the rubberised foam ingots, we knew we’d have to use one set per tower. They cannot be reused. They either have to be sent to landfill or burnt in the hole. The environmental impacts just weren’t right, particularly while constructing a renewable energy project like Murra Warra.”
“So, we suggested that we opt for metal reusable rings. Not only did these eradicate the environmental impacts, they gave us the benefit of being able to assemble the anchor cages in our factory and then shipping them to the site on the back of a truck.”
“We were able to provide an Australian-made solution. Our solution used all Australian steel and, on analysis, used 97% Australian content.”
Competing On Value And Innovation, Not Cost
“Allthread Industries was able to provide a quote that encompassed the cost of the steel plate and bolts finished and in the ground. When this was compared to the costs sighted by international suppliers, we were cost effective,” said Preston.
The total cost to buy and install anchor cage using Allthread Industries Australian-made anchors plus site labour costs was cheaper than using imported anchor cages plus site labour costs.
Rapid, Safe Construction
An Australian-Made Solution
Allthread Industries: The Trusted Australian Bolt Manufacturer
Established in Sydney in 1966, Sell & Parker metal recycling services has evolved over the years, making strategic acquisitions such as precision profiling (to merge with the already established Oxycut), AllThread Industries and First Forge. Today, the group plays a role in the entire steel lifecycle, supplying the mill with scrap, buying plate from the mill, and supplying bolts, plate and—in the case of Allthread Industries—assembled anchor cages to their customers.
Manufacturing from 2,400m² premises in Regents Park, New South Wales, Allthread Industries boasts over 40 pieces of plant including 20 specialised threading machines for sizes ranging from M5 to M120 in grades 4.6, 8.8 and 10.9 grade, as well as stainless steels in lengths up to 6m or longer by special arrangement.
Some of the products manufactured by Allthread Industries include hold-down bolts or anchor (foundation) bolts, bolt cages, square and round bottom J bolts, U bolts, rock bolts, threaded rod, nuts, washers and chemical anchors. As a trusted choice of some of the world’s largest brands such as Bechtel, CATCON, Downer and Thiess, Allthread Industries is proud to have remained at the top of its industry for more than five decades. While there is no re-inventing the bolt, technology is continuously evolving and improvements in steel, heat treatment, manufacturing and finishes have added a tremendous amount of customisation options. Allthreads’ engineers have the specialised knowledge and experience to manufacture custom designs for client needs.
“What sets us apart is our level of detail and engineering. We don’t just have thread rolling machines, operators and a production manager. We also have a strong and robust engineering department which, at the height of major projects, can include as many as eight engineers from a workforce of 40 people,” said Preston. “In addition to this, we deliver exceptional quality and adherence to ISO 9001. In fact, our engineering manager sits on the ISO standards committee for bolting and is currently reviewing a number of the latest standards for bolting. We’re not just focused on making a bolt to specification, we provide full traceability, inspection and testing. This means that when people buy from us, they don’t ever have to worry that what they’re buying might not be right. There is no such thing as a short cut at Allthreads.”