Allthread’s Australian-made wind-turbine anchor cages have numerous advantages over imported alternatives. They’re quicker, safer and easier to install, and cheaper when the entire cost (including transport and assembly) is included. Their environmental performance is also significantly better, with a recent independent Life Cycle Assessment finding the carbon footprint of Allthread’s cages to be around half that of their overseas-manufactured counterparts.
Pangolin Associates’ Life Cycle Assessment compared the environmental impacts of Allthread’s innovative, locally made and assembled anchor cages to that of similar cages manufactured in China and flat-packed to the site. Allthread’s cages had many significant benefits, including a 48% lower carbon footprint, and reductions of 133% and 89% in ozone layer depletion and minerals resources consumption, respectively.
‘We are thrilled to receive these results,’ said Simon Preston, Group General Manager of Allthread Industries. ‘This expert report shows there are huge environmental advantages to using locally-manufactured wind farm components, on top of the compelling construction and financial benefits.’
The exceptional environmental performance of Allthread’s anchor cages is due to several factors. The cages are made in Western Sydney using predominantly Australian materials, dramatically reducing emissions from shipping and other transport. Half of the factory’s electricity comes from solar power, further reducing greenhouse gas emissions. Allthread prioritises the use of both Australian and recycled material, reducing the environmental impact of transporting and manufacturing components.
Allthread pioneered the approach of preassembling anchor cages and delivering them to site, reducing the cages’ environmental impact and making them faster, easier, safer and more reliable to assemble. Allthread’s method dramatically reduces on-site assembly time, with the average cage taking less than four hours (less than two hours’ work for two people). In contrast, imported cages are shipped as flat packs from overseas and assembled on site from scratch, taking around 100 hours (six people working for two days using heavy machinery). Allthread’s assembly method is faster, easier, safer and more reliable.
All this adds up to significant benefits across a site. One example is the 38 anchor cages Allthread supplied to Victoria’s Murra Warra windfarm in 2021. All of the steel and 97% of the content used in the cages was Australian, while 50% of the content was also recycled. These anchor cages were approximately $200,000 cheaper than the imported alternative when the cost of installation and labour were included, (5% of anchor cage costs). Local manufacturing also allowed faster delivery, without the uncertainty of shipping. The first cage was delivered to site only seven weeks after the contract was signed, while the imported version would have taken around three months.
As well as a better environmental performance, Allthread’s solution offers other positives for Australia’s renewables transformation. ‘Each megawatt of wind energy generally consumes 60-100 tonnes of steel, much of which is currently imported’, Preston explains. ‘By encouraging the procurement of local products, Allthread can help our nation achieve a sustainable, economic energy transformation. As a NSW business leader and environmental enthusiast, this is something to which I’m deeply committed.’
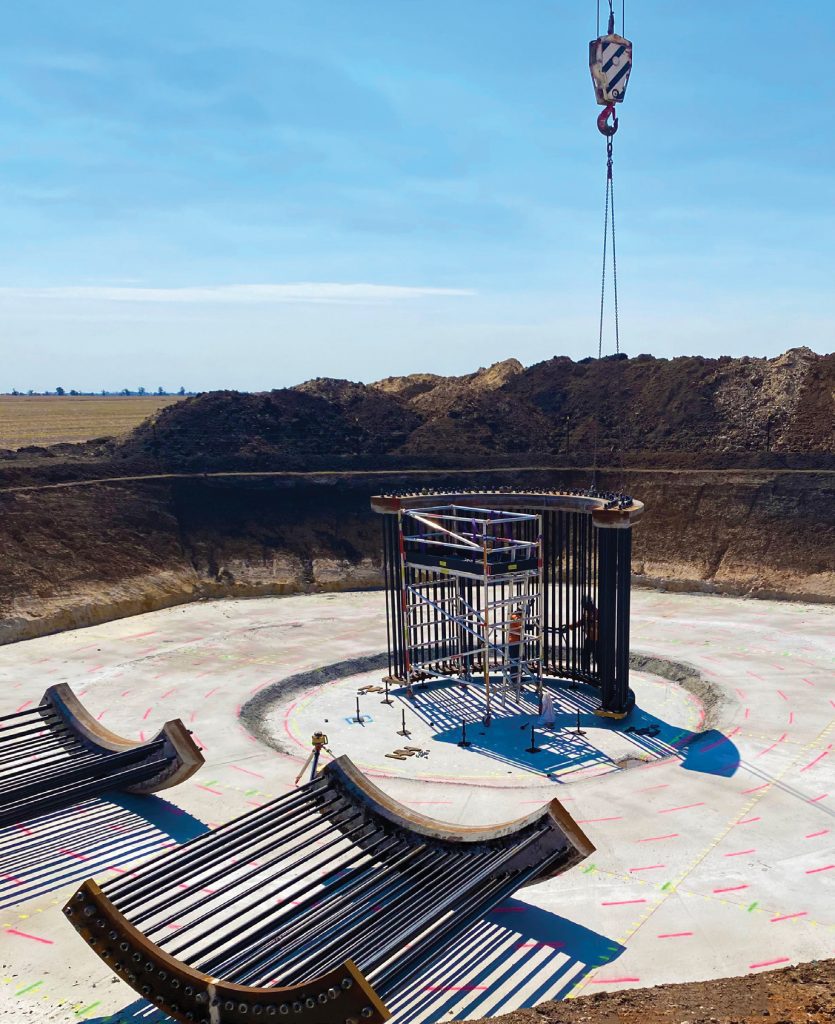